Were you aware of the amount of processes fabric goes through to get to the state that you see it in on your clothes? I certainly wasn’t! It is a common misconception that yarn is thread onto the knitting machine, where it then creates a roll of fabric which is then ready to use immediately in production. Unfortunately though, the process is not that simple. Below details the journey that cotton has to go through to ensure that it is suitable for you to wear it.
The many (28) processes cotton goes through from plant to fabric
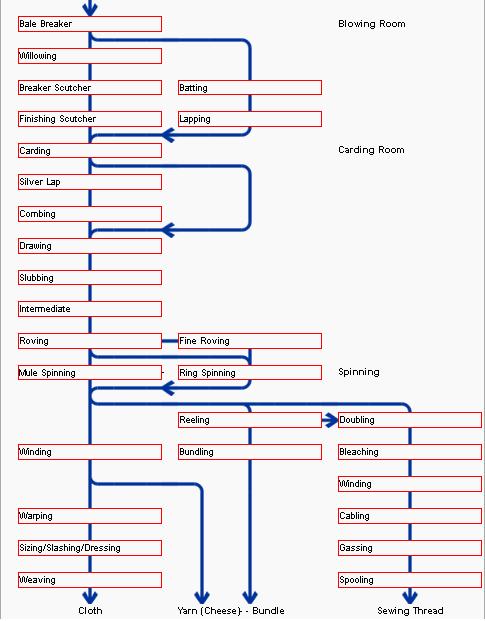
Spinning
Blowroom – This is the first stage of the process where the supplied, compressed bale (of cotton) is turned into a uniform lap of particular length. This is done by opening the material, cleaning it, removing any dust, blending of fibre material if needed, and feeding the material evenly to the card.
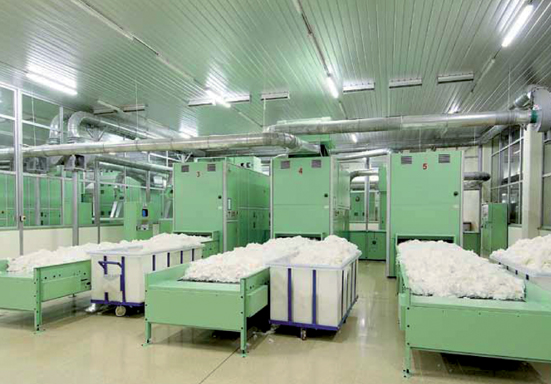
Carding – Carding is the most important process in spinning. It contributes a lot to the yarn quality. Fibres are passed between differently moving surfaces covered with card clothing (a very sturdy fabric with a leather or rubber fillet imbedded with wire teeth for disentangling and cleaning textile fibres). This breaks up clumps of fibre and aligns the individual fibres to be parallel with each other, producing a continuous sliver suitable for subsequent processing.
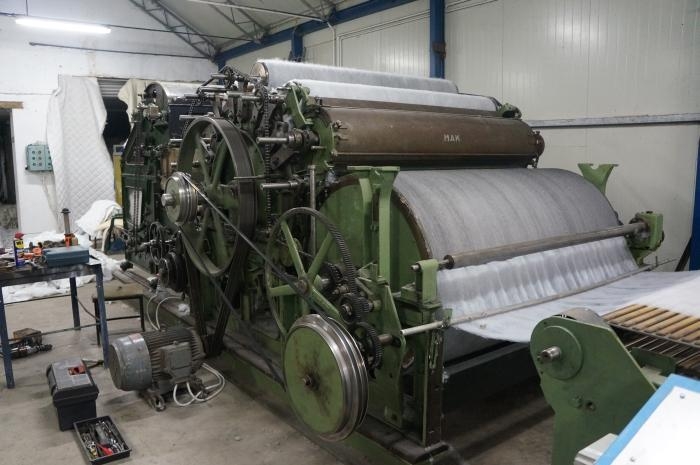
Drawing – Slivers are blended, doubled and levelled. This straightens fibres out, and makes them all uniform.
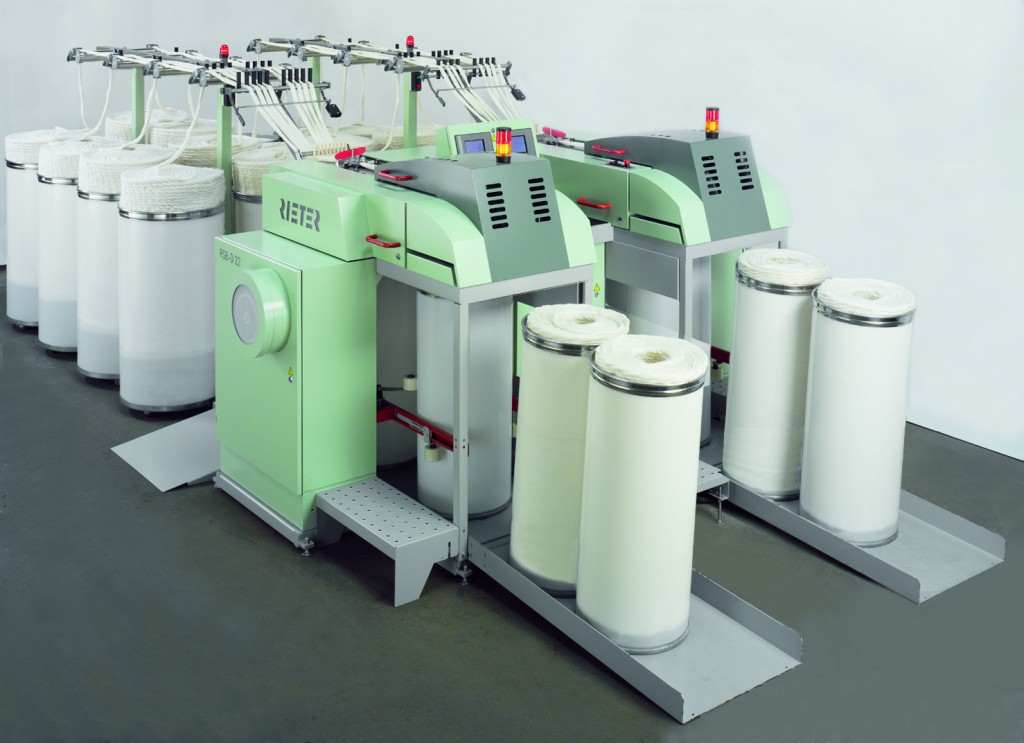
Combing – This creates uniform fibres, removing short fibres and creating uniform slivers.
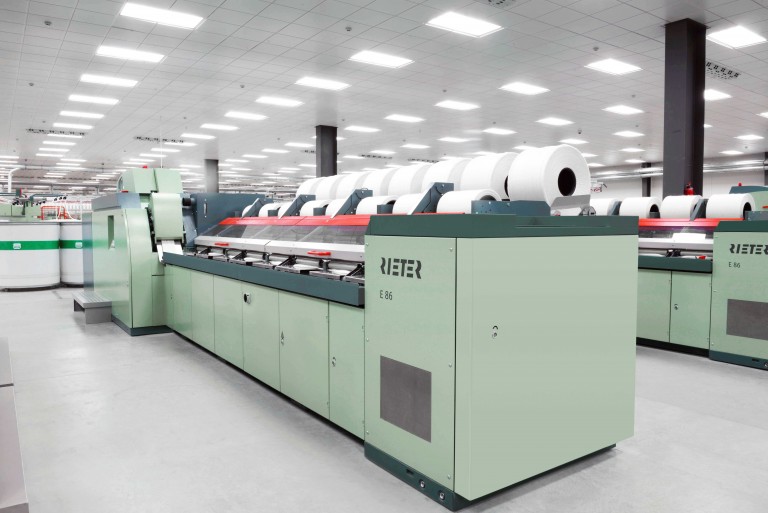
Drawing – Drawing is repeated. Slivers are blended, doubled and levelled. This straightens fibres out, and makes them all uniform.
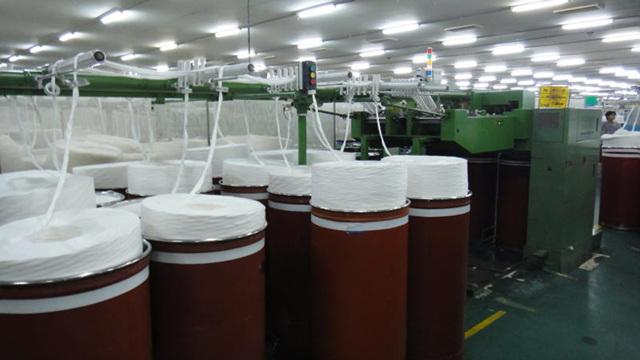
Roving Manufacturing – This reduces the weight per unit length through drafting, slightly twisting the slivers to add strength, and winding the twisted fibres (roving) onto a bobbin.
Simplex machine
Ring Spinning – The roving filaments are fed into a ring frame. The filaments are spun by chemical spinning. These filaments are solidified in fibre form. These solidified filaments are brought together and are slightly twisted to produce filament yarns. The different types of chemical spinning used to do this are wet spinning, dry spinning, melt spinning, bi-component spinning, and bi-constituent spinning.
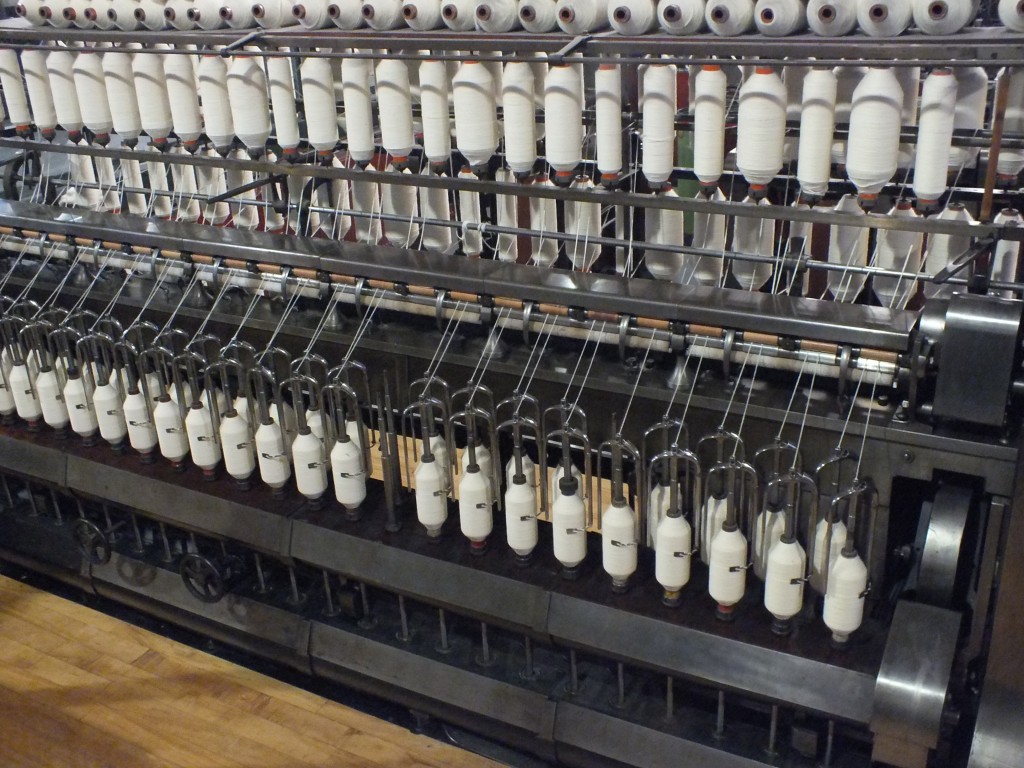
Weaving
Yarn from Spinning Section – If you want to make a yarn, you have two methods, carded yarn manufacturing and combed yarn manufacturing. Combed yarn is finer than carded yarn because it goes through more processes. The yarn produced by ring spinning is wound to produce a large package.
Carded yarn
Doubling and Twisting – This process twists 2 or more single threads to create a sewing thread wound around a bobbin by twisting them to increase strength and smoothness using a double ring frame.
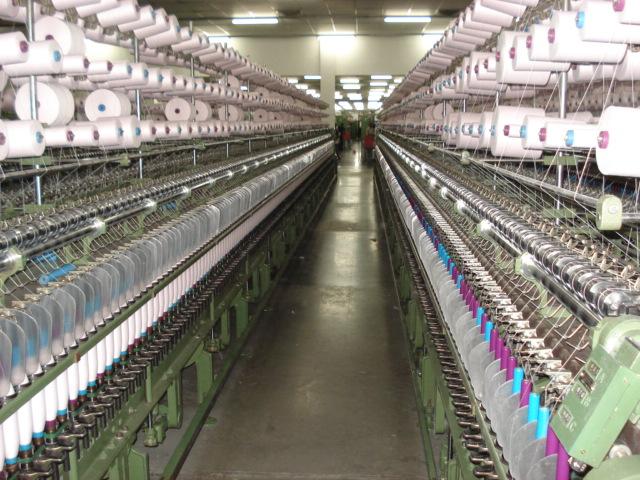
Winding – Winding is the process of transferring yarn or thread from one type of package to another to facilitate subsequent processing. There are two types of winding machines: precision winders and drum winders.
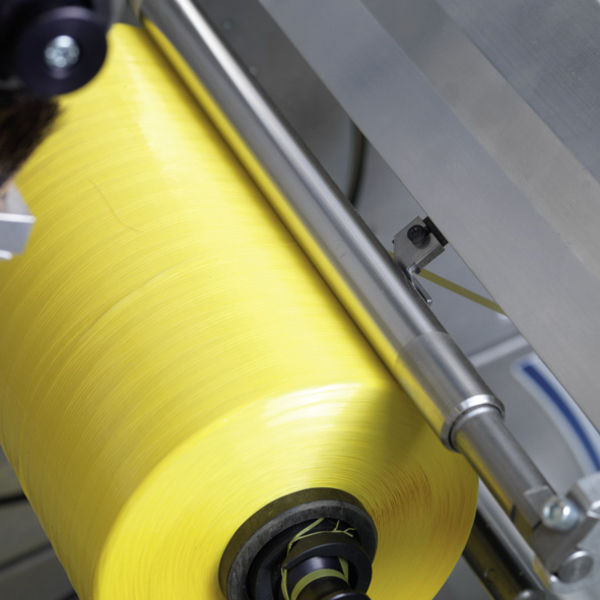
Creeling – Independent of the warping system, the threads are fed from bobbins placed on creels. The creels are metallic frames on which the feeding bobbins are fitted. They are equipped with yarn tensioning devices and yarn breakage monitoring systems. The creel capacity today usually amounts to 800-1200 bobbins.
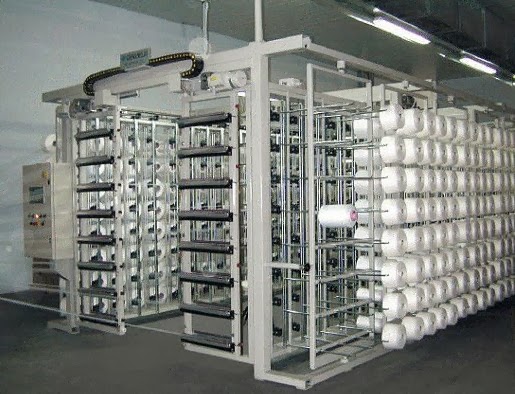
Warping – Warping is the parallel winding of yarn from a cone or cheese package on to a warp beam. The operation of winding warp yarns onto a beam is usually in preparation for slashing, weaving or warp knitting.